Why Don’t You Use Pressure-treated Wood to Repair Sagging Floors?
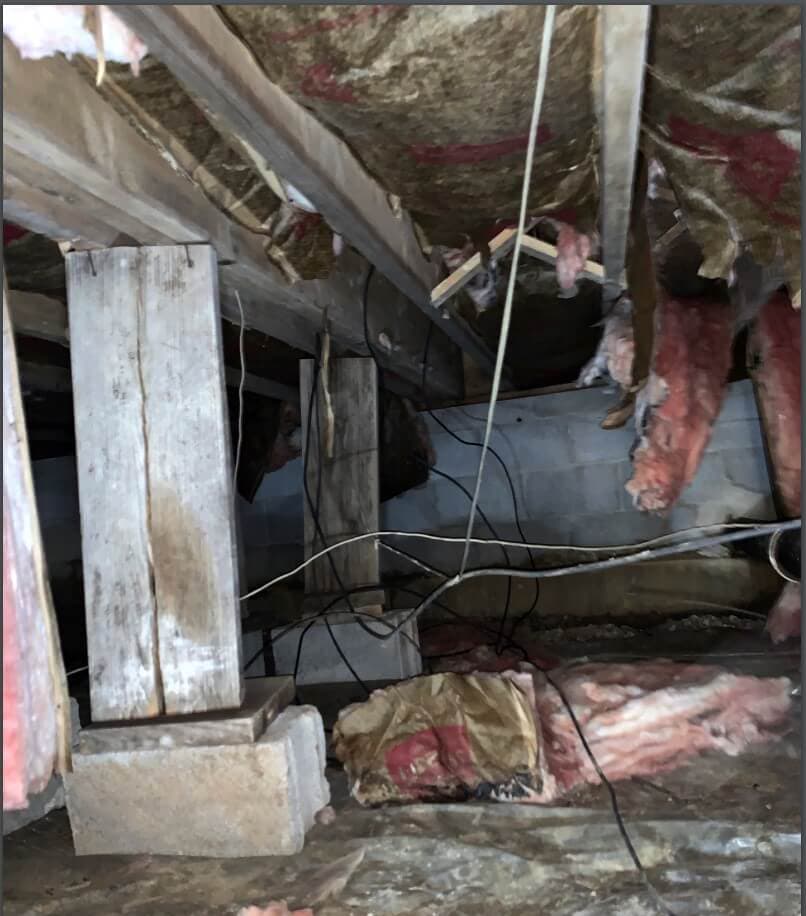
Originally posted 12/8/21; updated 12/22/22
On the surface, pressure-treated lumber seems like the ideal material for home construction. It’s resistant to both insects and rot, making it more durable and less prone to damage. So why don’t foundation repair companies use it for everything?
Acculevel is a family-owned and operated company that specializes in waterproofing and foundation repair. Since our start in 1996, we’ve helped over 35,000 homeowners restore their homes to optimal health and stability. We understand the importance of your home’s safety and value, and our goal is to provide a whole-home solution that preserves your home for years to come.
In this article, we’re going to explore what pressure-treated lumber is, what its ideal purpose is, and why it’s not commonly used to repair sagging floors.
What is Pressure-treated Lumber?
Pressure-treated lumber, sometimes referred to as pretreated lumber, is wood that has been soaked through with chemical preservatives. These additives are forced into and through the wood with high pressure.
This chemical infusion is done to make the lumber resistant to rot and insects. Because of the complete saturation, there is a prolonged drying time after the treatment. In fact, pressure-treated lumber is often still damp when it arrives at lumber yards.
Your Safety is Essential
Obviously, any home improvement should be done with safety of foremost importance. But if you are working with pressure-treated lumber, there are additional safety concerns you need to consider. Because there is a high concentration of chemicals in this lumber, you need specific PPE (protective personal equipment). At a minimum, you need an N95 mask to protect your respiratory system & goggles for eye protection.
The pretreated wood is tougher to cut and shape than standard un-treated lumber. You also need to keep any scraps or sawdust from this process separate from any “standard” lumber debris. Pressure-treated lumber should not be burned; dispose of any scraps or debris in a landfill. If you burn this wood, it will release toxic fumes and harm anyone that breathes them in.
What is Pressure-treated Lumber Used to Build?
Pressure-treated lumber is designed primarily for outdoor projects that are routinely exposed to the elements. These include items like decks, swing sets, or fences. All of these structures are placed out in the open, so the added protection from both rot and insects is invaluable.
While it is possible for the lumber to give off some small amounts of vapor as it dries, the great outdoors provides all of the ventilation needed.
Why Don’t Builders Use Pressure-treated Lumber for Homes?
Construction companies don’t use pressure-treated wood to build homes because it’s unsafe. The preservatives that are added to the lumber are highly flammable. If you have a house fire, treated lumber would accelerate the burn rate and give off highly toxic fumes. (Remember- this is why scrap wood and sawdust have to be discarded in a landfill!)
Additionally, if and when these pressure-treated components begin to break down, they could release harmful vapors. If a structure is entirely outdoors, that’s not a significant concern. But if all of the lumber used throughout your home is pressure-treated? That’s another story altogether! Houses are designed to keep out the cold, so they would trap those fumes inside.
The only exception to this rule is wooden components that have direct exposure to the ground.
Your Sill Plate Should Be Pressure-Treated Wood
The sill plate is the piece of lumber that connects your concrete foundation to the wooden flooring structure. This means it has direct and constant contact with the foundation.
This is a diagram of your home’s flooring structure. The sill plate is the board directly on top of the foundation, and the floor joists rest on top of it.
Both wood and concrete are porous materials that allow water to seep into and through it. This wicking action means that water from the ground outside your home can seep into the foundation and then into the wooden sill plate. From there, the sill plate can rot and transfer the moisture and decay to the floor joists.
In the example below, the homeowner reported that his floor was sloping towards the outside of his home. This is because the wooden components had gotten wet, causing them to decay and compress.
This photo was taken by an Acculevel project advisor during a free in-home assessment. You can see the sill plate, band joist, and floor joists are all rotting.
To repair the flooring structure, the band joist and floor joists needed to be sistered and the sill plate had to be replaced. To protect the homeowners’ well-being, the joist repairs are done with untreated wood. Only the sill plate is pressure-treated, limiting the potential for chemical exposure.
This photo was taken by an Acculevel crew member at the same home, after repairs were made. You can see a dramatic difference in the quality of the wooden components.
Sistering joists means attaching healthy new lumber to the failing component(s). Joists can’t be removed and replaced without significantly damaging the subfloor. You can learn more about repairing a sagging floor here.
How Does Pressure-Treated Lumber Affect Your Sill Plate?
Generally speaking, flooring structure repairs should be made with the same size of lumber. This causes the least amount of change to the structure, minimizing how much the subfloor has to shift to accommodate it.
However, pressure-treated lumber is always going to be slightly larger than untreated lumber. The chemicals added during treatment cause the wood to swell a small amount. This may seem like an inconsequential difference, but it’s enough to create some movement in the overall structure.
It is possible that you will experience some issues with cracking drywall or sticking doors after the repairs are complete. Your floor didn’t sag overnight- it took time to sink and bend, so it won’t immediately settle into position. Over time, the repaired flooring will adapt and be less intrusive.
Want More Information about Sagging Floor Repairs?
If you have noticed any sloping, sagging, or low spots in your home’s flooring, we can help! Our free guide to crawl space repairs answers all of the most commonly asked questions about damaged flooring structures and how to repair them. Some components, like the sill plate, need to be replaced. Others, like floor joists, should be “sistered,” a form of shoring or reinforcement.
Our guide describes the warning signs that indicate your crawl space needs repairs, explores the causes of damage, best repair methods, and costs of each. Even if you do not live in our service area (our coverage map is here), this guide is a valuable resource available to every homeowner, for free. The best consumer is a well-informed consumer! The more you know about your home and what it needs, the more confident you will be when hiring the necessary contractor to make repairs.
Ready to Schedule an In-home Assessment?
Call Acculevel at 866-669-3349, or complete our online form. We’ll schedule an appointment for you with one of our project advisors. Our PAs are friendly, knowledgeable, and experienced experts who will listen to your concerns, and discuss what you have noticed about your home. They will thoroughly evaluate your home and foundation, document any signs or symptoms, and then review this information and their diagnosis with you. Together, you will determine what the best whole-home solution is for you.
Acculevel’s goal is to provide 5 star customer service from start to finish. It begins the moment you contact us, continues through your home’s assessment and repairs, and extends all the way through our best-in-the-industry warranty program. We want you to help you preserve and protect your home for years to come.